Machinability refers to the ease with which a material can be cut or shaped using various machining processes. It determines how effectively a material can be worked into a desired shape through operations such as milling, drilling, or turning. Simply put, machinability tells you how easily a material can be manipulated using cutting tools. Understanding machinability is crucial for selecting the right tools and techniques to achieve efficient, precise, and cost-effective results in any machining process by SawbladeUniversity.
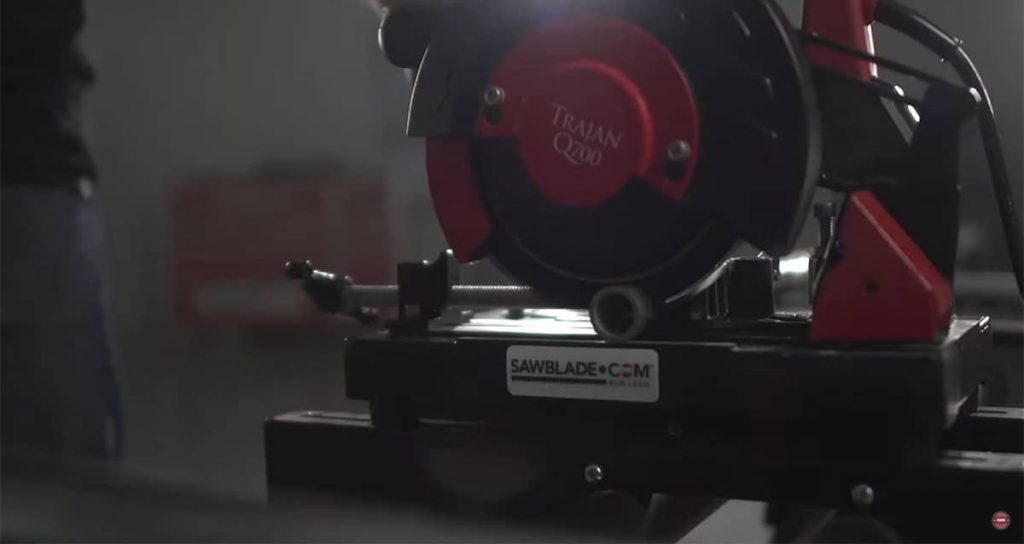
Test Your Knowledge on Machinability at Sawblade University
Want to put your understanding of machinability to the test? Head over to SawbladeUniversity.com and take the quiz on “What is Machinability?” This fun and interactive quiz will help you explore key concepts like material properties, cutting speeds, and how different factors influence the machining process. Whether you’re a seasoned machinist or just starting out, the quiz is a great way to assess your knowledge. Visit Sawblade University today and challenge yourself!
Key Factors That Influence Machinability
Machinability is affected by several factors, which together define how a material responds during cutting operations. Some of the most critical factors include:
- Material Properties: Hardness, strength, and thermal conductivity play a significant role in determining how easily a material can be machined.
- Cutting Tools: The type and quality of the cutting tool used directly impact machinability. Tools made of harder materials or those with specific coatings can improve cutting efficiency.
- Cutting Speed: The speed at which a tool moves across the material surface can either enhance or hinder machinability. Higher speeds often reduce friction and heat, improving the ease of cutting.
- Feed Rate: How quickly the material is fed into the cutting tool also affects machinability. Adjusting the feed rate ensures smoother cuts and prevents tool wear.
- Temperature: The heat generated during machining can influence the cutting process, with some materials becoming easier to work with at higher temperatures while others become more challenging.
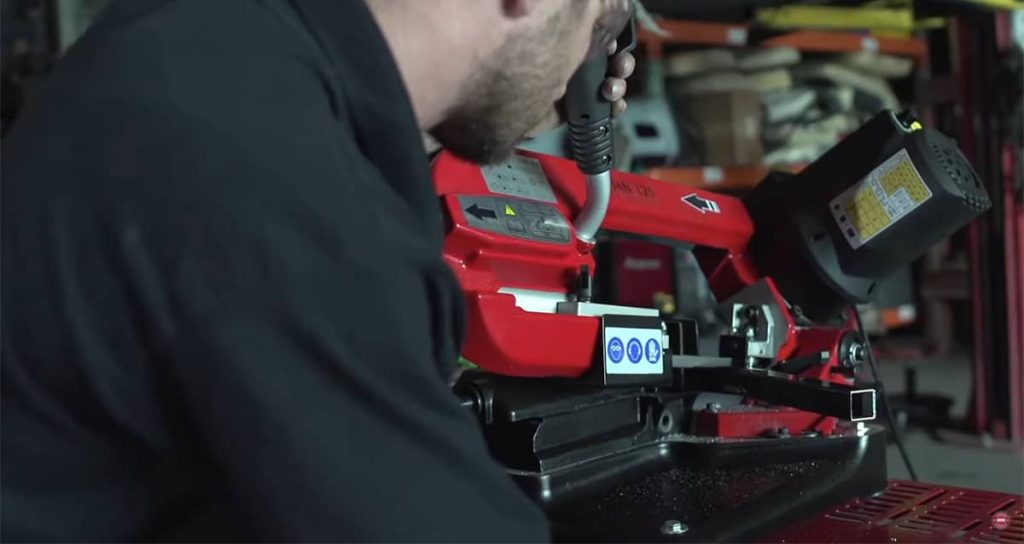
Material Machinability Ratings
Materials are often rated based on their machinability. These ratings provide insights into how well a particular material can be machined compared to a standard reference material. Generally, softer metals like aluminum have higher machinability, while harder materials like titanium or stainless steel are more difficult to machine.
Advanced Techniques to Improve Machinability
For materials that are harder to machine, certain techniques can be applied to improve the process. These include:
- Using Lubricants and Coolants: Applying coolants reduces the heat generated during cutting, which helps maintain tool sharpness and improves surface finish.
- Choosing the Right Tool: Opting for specialized cutting tools designed for tough materials can enhance machinability and reduce tool wear.
- Adjusting Feed Rates and Speeds: Calibrating the feed and cutting speeds can optimize the cutting process, especially for metals that are prone to work hardening.
Machinability of Common Metals
Material | Machinability Rating | Key Characteristics |
---|---|---|
Aluminum | High | Soft, easy to machine, requires lower cutting force |
Stainless Steel | Medium to Low | Tough, requires higher cutting force, work hardens |
Titanium | Low | Very strong, tends to generate heat during machining |
Brass | High | Easy to machine, excellent surface finish potential |
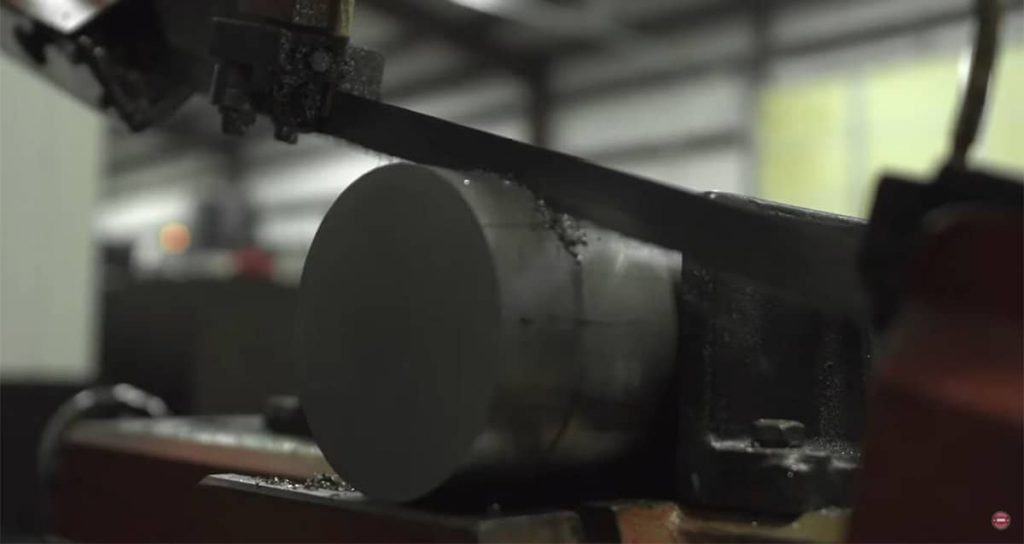
Why Machinability Matters
Understanding machinability helps machinists select the right tools and settings to achieve efficient cutting processes. High machinability translates to faster production times, reduced tool wear, and better surface finishes. On the other hand, poor machinability increases costs, requires frequent tool changes, and may lead to suboptimal results.
Watch the “What is Machinability?” Video on YouTube
Want a deeper understanding of machinability? Check out the “What is Machinability?” video by SawbladeUniversity.com on YouTube. This informative video explains the key concepts behind machinability, including factors like material properties, cutting tools, and machining techniques. It’s a great visual resource for anyone looking to learn more about how different materials are shaped and machined. Head over to YouTube now and watch the video to enhance your knowledge!
Learn More About Titanium
Curious about another essential metal used across industries? Discover the unique properties and applications of titanium in our article, “What is Titanium?” This lightweight yet incredibly strong metal is known for its corrosion resistance and wide use in aerospace, medical, and industrial applications. Explore how titanium compares to other metals like nickel and why it’s such a valuable material in various high-performance environments. Check out the article to deepen your knowledge of titanium and its incredible versatility.
Machinability is a crucial concept in the machining process, dictating how easily materials can be cut and shaped. By considering factors such as material properties, cutting tools, and machining speed, operators can optimize their processes for better performance. For anyone working with metal cutting or fabrication, understanding machinability ensures more efficient and cost-effective operations.