Band Saw Cutting of Inconel Alloys
An industrial bandsaw precisely cutting Inconel alloy, demonstrating controlled blade speed, efficient coolant flow, and steady feed rate for effective handling of this challenging material.
Why Cutting Inconel is Challenging:
Inconel is renowned for its high nickel content, offering exceptional rust resistance and strength. However, its high Rockwell hardness presents considerable challenges for metal cutting. This superalloy is popular in aerospace, oil and gas, and various industrial applications, demanding specialized techniques for efficient processing. Employing proper cutting practices ensures optimal productivity and extends equipment life, providing consistent results for your projects.
Band saws are especially effective tools for managing Inconel cutting tasks due to their precision, flexibility, and control. Selecting suitable blades and adhering to best practices is essential for operators working regularly with Inconel.
Recommended Techniques for Cutting Inconel:
To successfully cut Inconel, follow these proven techniques:
- Select the Right Blade: Carbide blades such as the Q1002 Triple Chip Carbide Blade with a 2-3 pitch are ideal. This specific blade effectively handles 7-inch diameter by 1.5-inch wall thickness materials, completing cuts within approximately 20 to 25 minutes.
- Control Blade Speed: Maintain blade speeds near 70 surface feet per minute (SFPM), helping reduce heat generation and blade wear while enhancing precision.
- Optimal Feed Rates: Aim for a cutting rate of about 0.5 to 1 square inch per minute, ensuring steady progress without blade overheating.
- Efficient Coolant Usage: Consistently applying quality coolant prevents heat buildup, reduces friction, and significantly extends blade life.
Blade Selection is Essential for Efficient Inconel Cutting
Choosing the proper blade significantly influences cutting success. Carbide-tipped blades like the Q1002 Triple Chip are specifically designed for high-hardness materials like Inconel, providing excellent durability and reduced cutting times. These blades maintain sharpness, ensuring consistently clean cuts and prolonged blade performance.
Optimal Band Saw Speeds and Feeds for Inconel Cutting
To achieve efficient Inconel cuts, your bandsaw must be correctly adjusted. Operating at approximately 70 feet per minute with the correct carbide blade ensures precise cuts while minimizing blade damage. Maintaining steady, moderate feeds helps sustain blade integrity and reduces production downtime.
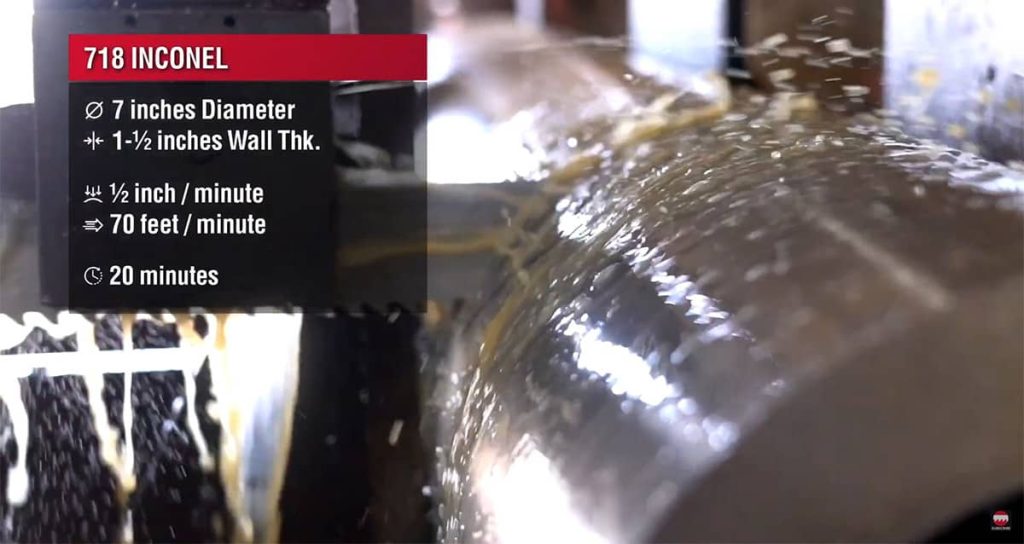
Recommended Band Saw Settings and Blade Type for Cutting Inconel:
Parameter | Recommended Settings |
---|---|
Blade Type | Q1002 Triple Chip Carbide Blade |
Blade Pitch | 2-3 pitch for 7” x 1.5” wall material |
Cutting Speed | Approximately 70 SFPM |
Cutting Rate | 0.5 to 1 square inch per minute |
Coolant | Consistently applied quality cutting fluid |
Blade Tension | Set according to manufacturer guidelines |
Improve Productivity and Minimize Downtime:
Using recommended blades and settings dramatically decreases downtime and increases productivity. Regular inspections, immediate replacement of worn blades, and optimal coolant use allow uninterrupted cutting operations, providing reliable, consistent output for demanding Inconel applications.
Maintenance Best Practices When Cutting Inconel:
- Frequently inspect blade edges for wear or damage; replace as needed.
- Regularly verify proper blade tension and alignment.
- Continuously apply coolant during cutting operations to manage heat.
- Keep the cutting zone clear of metal debris for optimal blade performance.
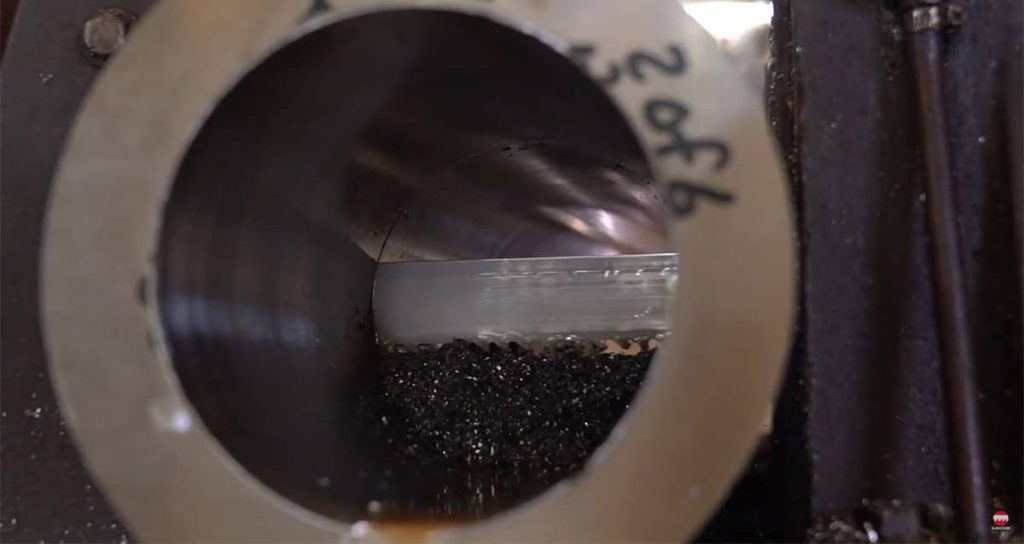
Consistent Precision for Demanding Applications
Inconel’s unique characteristics demand precise cutting capabilities. Band saws, especially when equipped with specialized carbide blades, provide reliable accuracy essential for applications in aerospace, oil and gas, and related industries. Using recommended blades, speeds, and maintenance ensures predictable outcomes and superior finished products.
Common Applications for Inconel 718:
- Aerospace engine components
- Oil and gas exploration equipment
- Structural elements in high-temperature settings
- Available forms include tubing, solid stock, structural sections, and extrusions
Immediate Enhancements to Your Cutting Process
Adopting these proven cutting practices leads to immediate improvements when working with Inconel. Correct blade selection, controlled speed adjustments, and dedicated maintenance greatly enhance cut quality and efficiency, contributing positively to your overall project results.
Summary of Benefits with Proper Inconel Cutting Methods:
- Extended blade lifespan and fewer blade replacements
- Reliable accuracy and improved cutting finish
- Increased production speed and efficiency
- Reduced downtime through proper equipment care
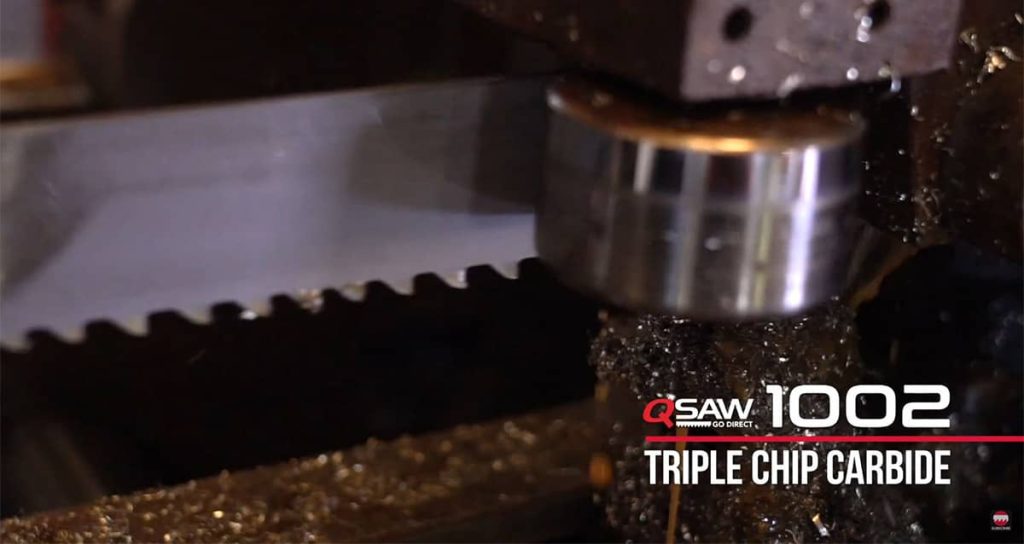
Enhance Bandsaw Performance Further with the Q701 M71 Blade
To further improve your bandsaw’s cutting efficiency, read our related article, “Performance and Accuracy Combined: The Q701 M71 Blade Difference”. Learn how upgrading your bandsaw blade to the Q701 M71 delivers higher accuracy, durability, and productivity especially suited for tough alloys like Inconel.
Maximize Bandsaw Efficiency with Simple Preventive Maintenance
Ensuring your bandsaw stays in excellent condition requires routine care and attention. To maintain peak performance and extend your equipment’s lifespan, read our article, “Preventive Maintenance Tips for Keeping Your Bandsaw in Top Condition.“ You’ll find straightforward strategies and easy-to-follow guidelines on blade care, routine inspections, and maintaining proper machine adjustments helping you avoid unnecessary downtime and achieve consistent cutting accuracy.
Preserve Your Equipment, Optimize Your Results:
Applying these Inconel cutting best practices ensures optimal blade life, reduces machine wear, and delivers consistently high-quality cuts. Regular maintenance is simple yet provides significant, lasting improvements, helping you maintain efficiency and excellence in your metal fabrication operations.