Understanding the Role of Maintenance in a Fabrication Shop
Tool maintenance has always played a key part in keeping production consistent and efficient. In fabrication environments, downtime caused by malfunctioning machines can lead to unexpected delays, higher costs, and safety risks. That’s why building a solid maintenance routine is one of the best ways to keep tools ready for daily use and reduce the chances of failure.
Fabrication shops rely on a wide range of cutting, shaping, and assembly tools to stay productive. Each machine, from bandsaws to press brakes, performs best when maintenance is part of the daily or weekly workflow. With the right approach, you can reduce breakdowns and support a smoother, safer operation.
What Preventive Maintenance Can Help You Avoid
Preventive maintenance is one of the most effective ways to extend the performance and reliability of your machines. Here are some of the problems it can help avoid:
- Unexpected breakdowns that stall production
- Costly repairs due to ignored wear or loose components
- Safety issues related to worn-out guards, dull blades, or damaged switches
- Poor cut quality or reduced accuracy
- Lost time troubleshooting preventable issues
- Equipment that fails before its expected service life
Why Maintenance Matters More Than Ever
Fabrication shops run on tight schedules. Delays caused by equipment failure can affect deadlines and profitability. In some cases, even a short pause in production can set back the entire job. A consistent maintenance routine helps reduce interruptions, improves safety, and allows your team to rely on their tools day after day.
Key Maintenance Tasks Every Fabrication Shop Should Include
- Clean tools daily to remove chips, dust, and oil
- Check alignment and calibration of moving parts
- Tighten fasteners and secure guards
- Inspect blades, belts, and other consumables
- Lubricate pivot points, bearings, and gears
- Replace worn parts before failure occurs
- Document all maintenance activities for traceability
The Cost of Downtime in Machine Shops
A single piece of equipment sitting idle can affect the entire process. In some shops, unexpected downtime has been shown to reduce productivity by as much as 40%. This impact isn’t limited to repair costs it also includes lost labor time, rescheduling, and missed deadlines. Staying ahead with regular tool checks is a reliable way to avoid these disruptions.
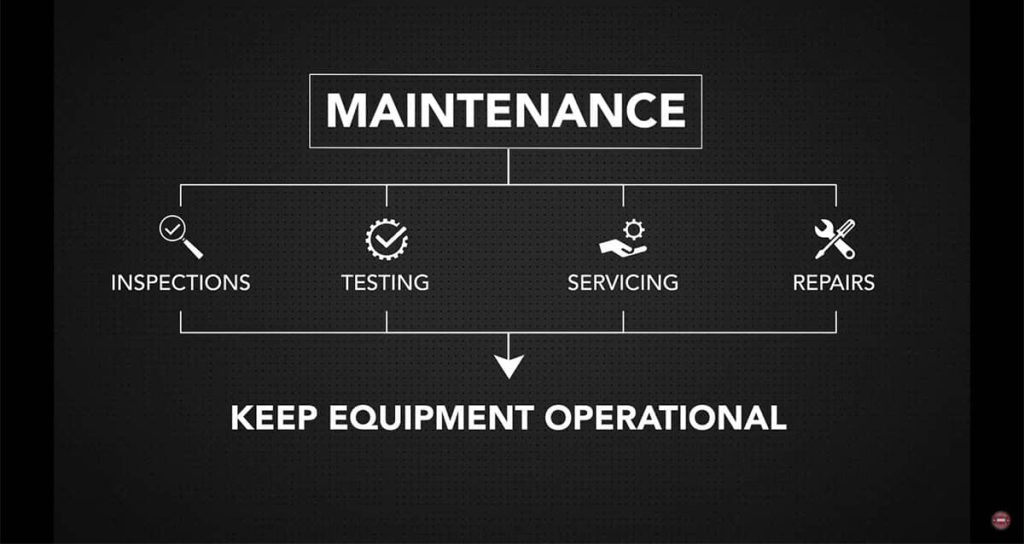
Finding the Right Approach for Your Shop
There isn’t one universal solution to tool maintenance. Some shops benefit most from preventive maintenance, while others may adopt a blended method with predictive tools or even reactive fixes for low-use equipment. What’s important is choosing an approach that fits your workflow, budget, and staff expertise.
Quick Comparison of Maintenance Styles
Approach | Description | Best Used For |
---|---|---|
Preventive Maintenance | Scheduled, routine servicing and inspections | Most fabrication shops with regular tool use |
Predictive Maintenance | Uses data/sensors to anticipate failures | Larger operations with high-value machinery |
Reactive Maintenance | Repairs only after failure | Low-cost or rarely used equipment |
Training Your Team for Long-Term Success
Even the best maintenance plan can fall short if your team isn’t trained. Clear guidelines, consistent checklists, and regular training sessions can help technicians and operators understand how to recognize early signs of wear, what needs routine servicing, and when to escalate issues to supervisors.
What Makes Preventive Maintenance So Cost-Effective
While regular service takes time and resources, it pays off in fewer repairs and extended tool life. By comparing the cost of ongoing maintenance to the downtime and replacement costs of reactive repairs, most shops find that preventive care quickly justifies the effort.
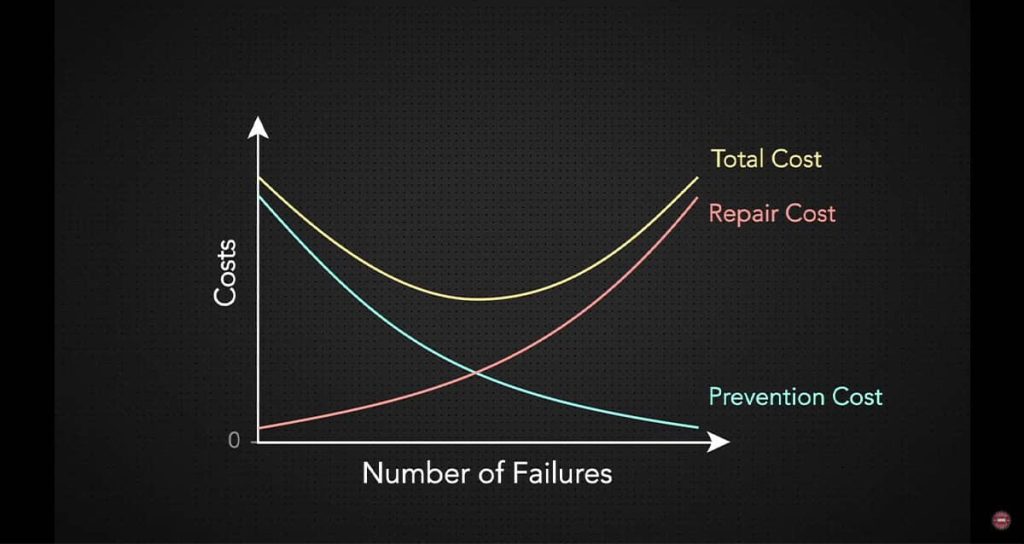
Simple Tools That Help Track Maintenance
- Wall-mounted checklists
- Maintenance logbooks
- Color-coded tags or stickers
- Digital apps that schedule reminders
- Barcode systems to scan when a task is done
Signs It’s Time to Service a Tool
- Unusual vibrations or sounds
- Decreased accuracy or output
- Loose or worn components
- Electrical issues like slow startups or flickering displays
- Visible dirt buildup or rust
- Tools that feel unsafe or unsteady
Best Practices from Shops That Maintain Tools Well
- Assign someone responsible for tool care
- Include cleaning and inspection in end-of-day tasks
- Set a clear weekly schedule for in-depth checks
- Keep replacement parts and lubricants on hand
- Review tool performance in weekly staff meetings
Test What You Know About Maintenance
Think you’ve got a solid grasp on why maintenance matters in a workshop? Put your knowledge to the test with our quick quiz on Understanding the Importance of Maintenance. Whether you’re just starting out or have years of experience, this short quiz will help you identify what you know and what you might still need to learn. It’s a great way to reinforce best practices and spot areas for improvement. Take the quiz now and see how you score!
Learn More About Cutting Advanced Materials
If you’re working with fabrication tools, you’ll eventually come across challenging materials that demand more than standard cutting methods. Curious about how unique alloys behave under the blade? Our article “What Are Exotic Alloys and How Are They Cut?“ breaks down what makes these materials different and explains the specialized techniques used to process them safely and efficiently. It’s a great read if you’re looking to expand your knowledge or prepare for precision jobs involving high-performance metals.
A Helpful Resource to Watch
Want to learn more about developing a maintenance strategy that fits your shop? We recommend the video “Understanding Preventive Maintenance.” It explains how this method works, why it reduces long-term costs, and how to build it into daily operations.
Keep Your Fabrication Shop Running Smoothly
Improving tool maintenance doesn’t require a full overhaul of your operations. It starts with small, consistent steps like checking machines before use, cleaning daily, and scheduling inspections. Over time, these habits can make a major difference in tool performance, employee safety, and project timelines. A well-maintained shop is a more efficient shop.