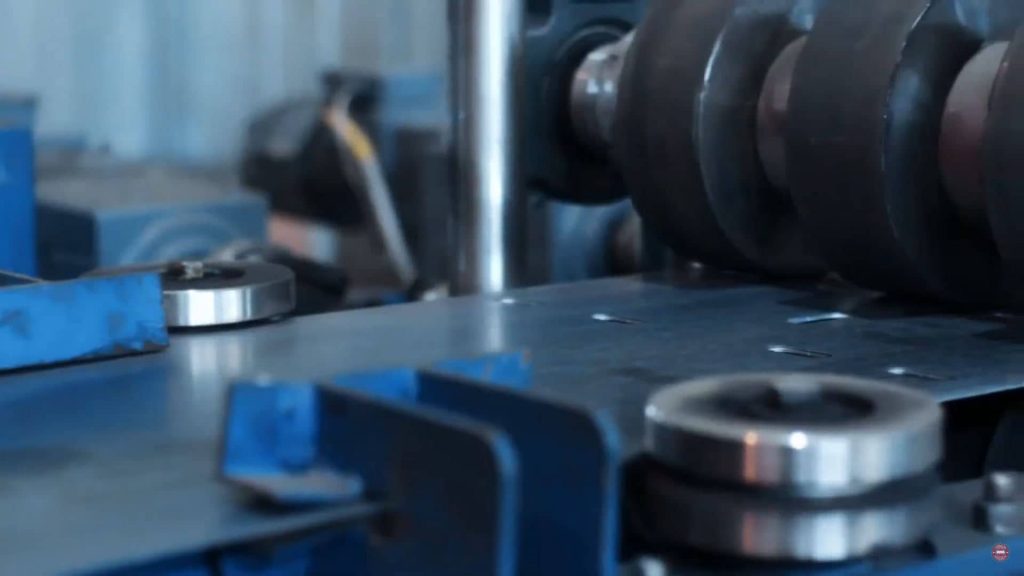
Have you ever wondered why some materials become stronger and harder after being shaped or deformed? This fascinating phenomenon is known as cold working. Cold working, also referred to as work hardening, is a process that involves deforming metals at room temperature to enhance their mechanical properties. Understanding cold working can help you appreciate the strength and versatility of metals used in various applications.
Statistics show that cold working can increase the strength of materials by up to 50%, making it a crucial process in manufacturing and metalworking industries. Cold worked materials exhibit enhanced properties such as increased hardness, yield strength, and improved surface finish, which are essential for high-performance applications.
But don’t worry – before you decide that cold working is too complex to understand, let’s break down its principles, benefits, and effects on materials.
What are the Benefits of Cold Working?
Cold working offers several advantages that make it a valuable process in the metalworking industry. Some of the key benefits include:
- Increased Strength and Hardness: Cold working increases the dislocation density in the material, leading to enhanced strength and hardness.
- Improved Surface Finish: The process refines the surface structure of the material, resulting in a smoother and more uniform finish.
- Enhanced Wear Resistance: Cold worked materials exhibit better wear resistance, making them suitable for high-stress applications.
- Cost-Effective: Cold working does not require heating, reducing energy consumption and costs associated with thermal processes.
These benefits make cold working an attractive option for manufacturing components that require high strength and durability, such as automotive parts, aerospace components, and construction materials.
What are the Components of Cold Working?
To effectively perform cold working, it is essential to understand the key components involved in the process. These include:
- Deformation Tools: Tools such as rollers, presses, and hammers are used to apply mechanical force to deform the material.
- Material Properties: The properties of the material, including its ductility and workability, play a crucial role in determining the extent of deformation.
- Dislocation Density: Cold working increases the dislocation density in the material, leading to strain hardening and improved mechanical properties.
All these components must be carefully controlled to achieve the desired level of deformation and enhance the material’s properties.
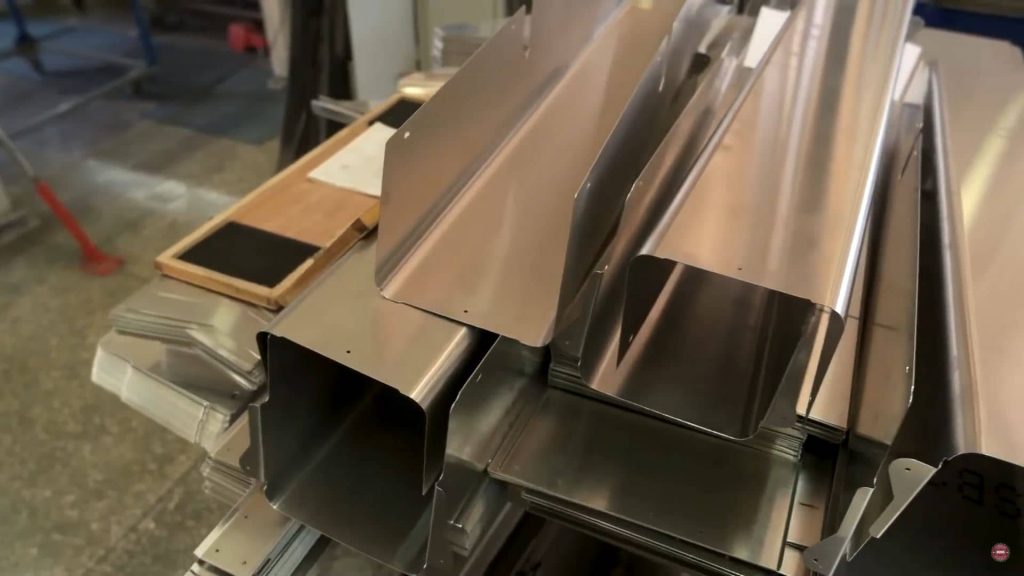
How Does Cold Working Affect Materials?
Cold working significantly alters the mechanical and physical properties of materials. The process involves the following key changes:
Increased Dislocation Density
Cold working introduces a high density of dislocations within the material’s crystal structure. Dislocations are defects in the crystal lattice that impede the movement of atoms, thereby increasing the material’s strength and hardness. This phenomenon, known as strain hardening, is a primary reason for the enhanced properties of cold-worked materials.
Grain Refinement
During cold working, the grains within the material become elongated and refined. This grain refinement contributes to improved mechanical properties, such as increased strength and hardness. Additionally, the refined grain structure enhances the material’s resistance to crack propagation and fatigue.
Impact on Material Properties
The changes induced by cold working have a profound impact on the material’s properties. Some of the notable effects include:
- Increased Yield Strength: Cold working raises the yield strength of the material, making it more resistant to deformation under load.
- Improved Hardness: The material becomes harder and more resistant to wear and abrasion.
- Reduced Ductility: While cold working increases strength, it also reduces the material’s ductility, making it more brittle and prone to fracture.
- Enhanced Fatigue Resistance: The refined grain structure and increased dislocation density improve the material’s resistance to fatigue failure.
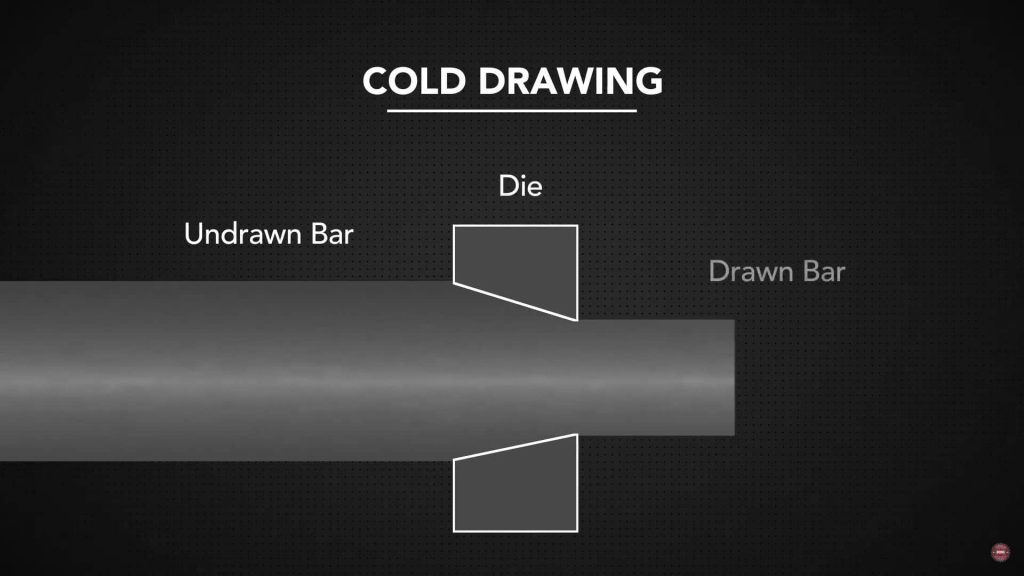
Applications of Cold Worked Materials
Cold worked materials are widely used in various industries due to their enhanced properties. Some common applications include:
- Automotive Industry: Components such as gears, shafts, and fasteners are often cold worked to achieve high strength and durability.
- Aerospace Industry: Cold worked materials are used in critical aerospace components that require superior mechanical properties and reliability.
- Construction Industry: Structural elements such as beams, columns, and reinforcing bars benefit from the increased strength and hardness provided by cold working.
Tips for Users
To make the most of tools and materials that have undergone cold working, consider the following tips:
- Choose the Right Tool: Select tools that are designed to handle the stresses of cold worked materials. Look for saw blades and cutting tools specifically engineered for enhanced durability and performance.
- Regular Maintenance: Regularly inspect your tools for signs of wear and tear. Cold worked tools may last longer, but they still require routine maintenance to perform optimally. Clean, sharpen, and lubricate your blades as needed.
- Proper Storage: Store your cold worked tools in a dry, secure place to prevent damage. Proper storage can extend the lifespan of your tools and ensure they remain in good working condition.
- Use Appropriate Cutting Techniques: When cutting cold worked materials, use techniques that minimize stress and avoid overheating. This can help maintain the integrity of both the tool and the material being cut.
- Safety First: Always prioritize safety by wearing appropriate protective gear, such as gloves, safety glasses, and hearing protection. Follow manufacturer guidelines for the safe operation of your tools.
Watch Our Video on Cold Working
For a deeper understanding of cold working and its impact on materials, check out our detailed video tutorial by Sawblade University. In this video, we cover the essential techniques and benefits of cold working, along with practical demonstrations to help you master the process. Click the link below to watch the video and enhance your knowledge and skills.
Ensuring Safety with Cold Worked Materials
While cold working enhances the properties of materials, it is essential to ensure safety during the process. Follow these safety tips when working with cold worked materials:
- Wear Protective Equipment: Always wear safety glasses, gloves, and appropriate clothing to protect yourself from sharp edges and flying debris.
- Use Proper Tools: Ensure that the tools used for cold working are in good condition and suitable for the task at hand.
- Maintain a Clean Work Area: Keep your work area clean and free from clutter to prevent accidents and ensure smooth operations.
By following these safety guidelines, you can safely perform cold working and achieve the desired enhancements in material properties.