When working with a bandsaw, one of the most important decisions you can make is selecting the right blade for the job. While material type and project requirements play major roles, understanding the coarseness of the blade is crucial. The coarseness, or the fineness, of a bandsaw blade directly impacts the speed, precision, and quality of your cuts. But what determines a blade’s coarseness, and how can you ensure you choose the right one for your work? Let’s dive into this essential aspect of bandsaw blades.
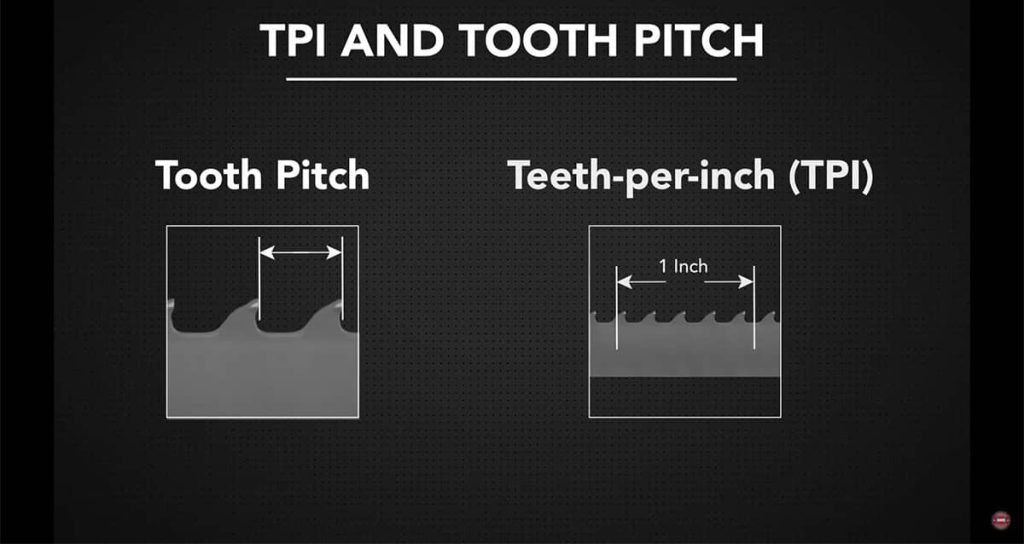
What Factors Define Blade Coarseness?
There are several factors used to rate the coarseness of a bandsaw blade. The primary measurement is Teeth Per Inch (TPI), which refers to how many teeth are in every inch of the blade. A low TPI indicates a coarser blade, which is designed for fast, rough cuts, especially in thicker materials. On the other hand, a higher TPI results in finer, smoother cuts, ideal for more detailed work on thinner materials. Tooth geometry and the material of the blade also contribute to its overall coarseness and performance.
Common TPI Ranges and Applications
- 3-6 TPI: Coarse blades for cutting thicker, harder materials such as wood or metal.
- 10-14 TPI: Moderate blades for versatile use across various materials, suitable for metal and woodworking projects.
- 18-24 TPI: Fine blades for cutting thin materials, including tubing and small-diameter metal pipes.
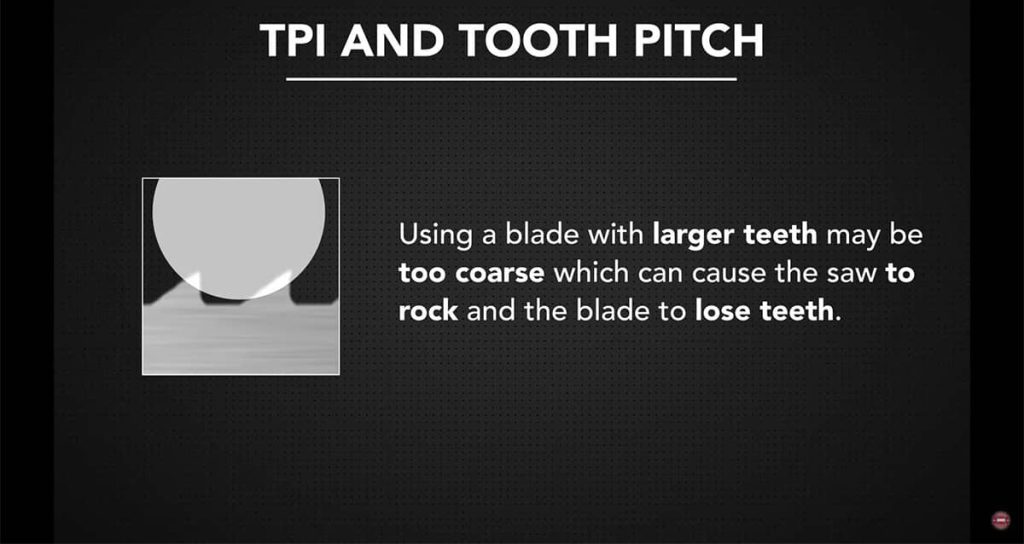
The Importance of Tooth Geometry
Tooth geometry is another key element that affects blade coarseness. The shape and arrangement of the teeth influence how effectively the blade cuts through materials. For instance, blades with aggressive tooth patterns like hook-tooth blades are more suited for cutting thick or hard materials, while regular-tooth blades are more versatile and better for general-purpose cutting. Skip-tooth designs work well with softer materials, such as non-ferrous metals and plastics, allowing for smoother finishes.
Importance of Minimum Teeth Contact for Smooth Cutting
When using a bandsaw blade, it’s crucial to ensure that at least three teeth are in constant contact with the material being cut. This rule helps maintain the stability of the blade and ensures cleaner, more precise cuts. If fewer than three teeth are in contact with the workpiece, the blade is more likely to snag or grab the material, leading to rough, uneven cuts or even damaging the blade. By maintaining the minimum of three teeth engaged, you reduce vibration and improve cutting accuracy, enhancing both the blade’s lifespan and the overall quality of your work.
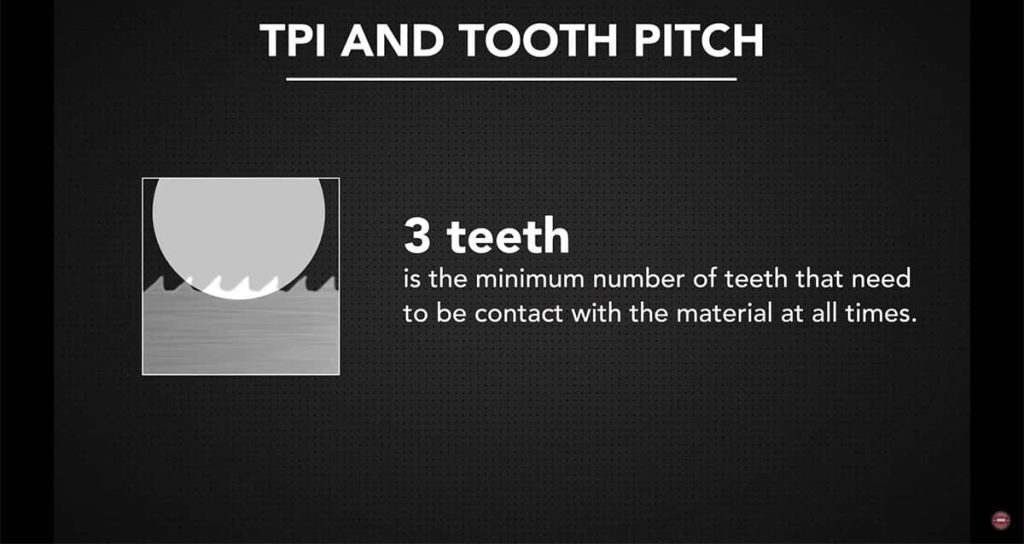
Choosing the Right Blade for Your Bandsaw
Selecting the correct bandsaw blade is about balancing speed and precision. If you prioritize faster cuts, especially when working on large materials, a coarser blade (with a lower TPI) is ideal. However, if you need clean, accurate cuts, particularly in delicate materials, a fine blade with a higher TPI will serve you better. Understanding your project requirements and the material you’re cutting helps in making the right choice.
Portable Bandsaw Specifications
Model | TPI Range | Cutting Capacity | Ideal Material | Speed (SFPM) |
---|---|---|---|---|
DeWalt DCS377B | 14/18 | 1 ¾ in. | Metal, plastic, wood | 150-380 SFPM |
Milwaukee M12 2429-21XC | 14-18 | 1 5/8 in. | Small diameter metal | 280 SFPM |
Milwaukee M12 2529-21XC | 12-16 | 2 ½ in. | Unistrut, EMT, metal | 350 SFPM |
Making an Informed Decision
To make the best decision, always consider the specific needs of your project. If you’re working on thick metal piping, a coarse blade with a lower TPI will provide the aggressive cutting action you need. For thinner materials like sheet metal or plastic, a fine blade with a higher TPI ensures cleaner, smoother cuts. Knowing the blade’s coarseness and how it matches your material is key to achieving optimal performance.
Benefits of Proper Blade Selection
- Improved Cut Quality: Choosing the right TPI ensures smoother cuts, reducing the need for post-cut finishing.
- Extended Blade Life: Matching the blade to the material improves its durability, minimizing breakage or premature wear.
- Efficiency: Proper blade selection enhances cutting speed, saving time and energy during your projects.
Test Your Knowledge on Saw Blades
Think you know everything about saw blades, TPI, and tooth pitch? Challenge yourself by taking the Understanding Saw Blades: TPI & Tooth Pitch quiz on SawbladeUniversity! This interactive quiz is perfect for sharpening your knowledge and ensuring you’re making the best choices when it comes to blade selection. Head over to SawbladeUniversity now and see how well you understand these critical concepts!
Discover More About Plain Carbon Steel
If you’re curious about the composition, numbering system, and various uses of plain carbon steel, don’t miss our detailed article, Plain Carbon Steel: Composition, Numbering System, and Uses. This informative guide covers everything from its basic properties to how it’s categorized, making it a valuable resource for anyone working with steel or looking to understand it better. Head over now to dive deeper into the essential facts about plain carbon steel and how it’s utilized in a wide range of industries!
In conclusion, the coarseness of a bandsaw blade, determined by factors like TPI, tooth geometry, and blade material, plays a critical role in the cutting performance. Whether you’re looking to make rough, fast cuts or fine, precise ones, selecting the right blade ensures you achieve the desired results while prolonging the life of your tool. By understanding these key elements, you can confidently choose the best blade for any project, ensuring both efficiency and quality in your cuts.