What Causes Bandsaw Blades to Twist
Blade twisting on a bandsaw is a problem many operators face, and it can disrupt cutting accuracy and wear out your machine prematurely. This usually happens when blades are installed incorrectly, stored poorly, or mismatched to the material being cut. A twisted blade won’t track properly, leading to inconsistent cuts and potential damage. Recognizing the issue early can help maintain smoother operation and prevent unnecessary tool wear.
Signs Your Bandsaw Blade Is Twisted
- Unusual noises like squealing or clicking during cuts
- Blade drifts or tracks off-center
- Teeth appear misaligned relative to the material
- Cuts are not straight or consistent
- Friction between the blade and guides or housing
How to Fix a Twisted Blade
To address a blade twist, start by removing the blade and inspecting it along a flat surface. Look for any kinks or uneven spots. Gently reshape the blade by hand if needed, being careful not to force it. Reinstall with care, checking that the blade runs evenly across both wheels and that the tracking is aligned. Tension should be firm but not excessive to avoid creating new twists.
Proper Blade Storage Matters
Blades that are bent or twisted often have been stored carelessly. Always coil blades carefully and store them in a flat position, away from damp or hot environments. Avoid sharp bends during uncoiling, and use gloves to stay safe and maintain control.
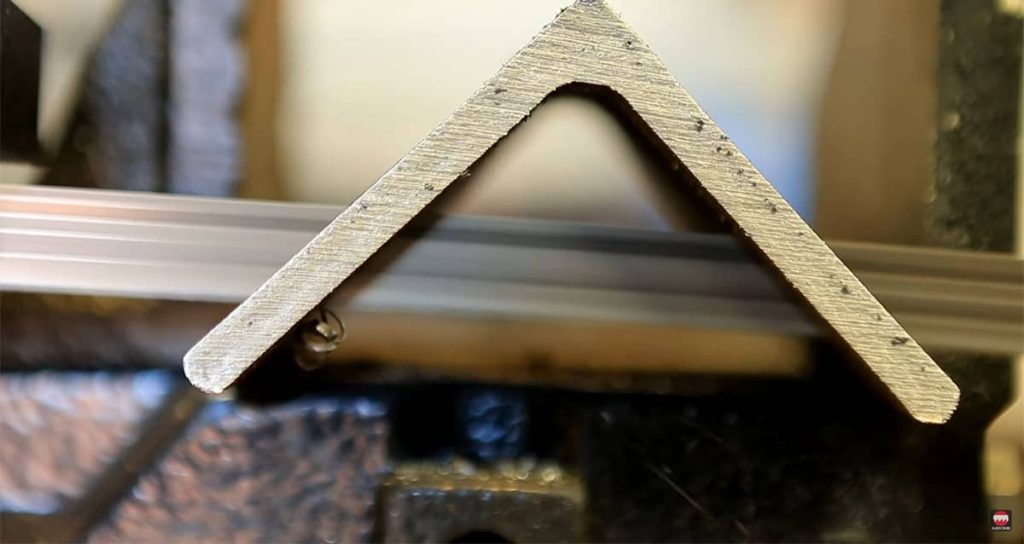
Recommended Tooth Pitch by Material Type
Material | Ideal Tooth Pitch (TPI) |
---|---|
2″ x 2″ Angle (3/8″ wall) | 4-6 or 3-4 |
Thin-Walled Tubing | 5-7 or 8-11 |
4″ x 4″ Box Tubing (3/8″ wall) | 4-6 |
4″ Solid Round Bar | 3-4 |
8″ Solid Round Bar | 2-3 |
Selecting the right pitch ensures the blade cuts efficiently with less strain. Coarser pitch is better for thick or dense materials, while fine pitch suits thin sections and helps avoid snagging.
Choose the Right Blade for the Job
Incorrect blade selection can lead to twisting, vibration, and poor results. Make sure your blade matches the type and thickness of the material, as well as your saw’s specifications. Blade width, tooth shape, and thickness should all align with the task for reliable cutting.
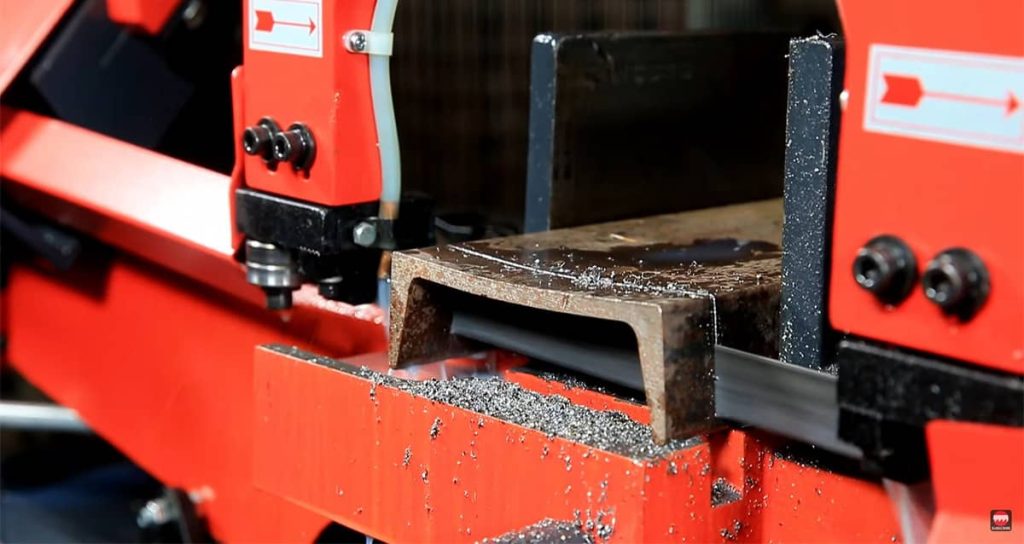
Simple Practices to Prevent Blade Twists
- Uncoil and coil blades gently
- Set blade tension to manufacturer recommendations
- Keep guides and blade supports clean and aligned
- Match blade pitch to material dimensions
- Always release blade tension when storing the saw
When It’s Time to Replace Your Blade
A blade that’s twisted repeatedly, cracked at the weld, or worn unevenly should be replaced. Continuing to cut with a compromised blade can put added stress on your bandsaw and reduce cut quality.
Smart Storage Techniques
- Store coiled blades on designated hooks or racks
- Keep them off the ground and out from under other tools
- Protect from humidity to prevent rust
- Mark blades after use to track condition over time
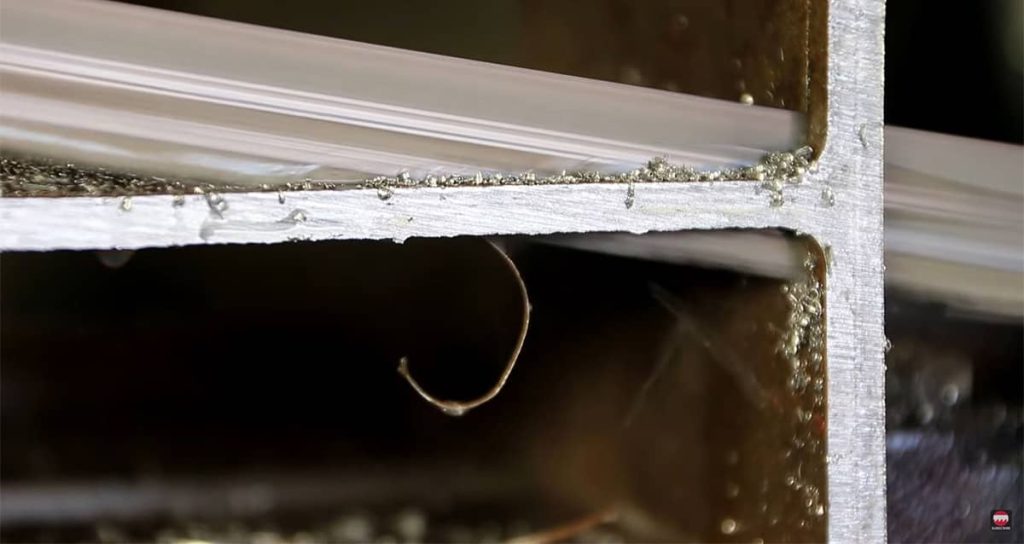
Get Expert Blade Advice Anytime
If you’re unsure which blade is right for your material or setup, visit Sawblade.com for detailed recommendations, product specs, and video guides. Their support can help you find the best option for structural steel, tubing, solid bar, and more.
Unsure About Blade Sizing for Your Bandsaw?
Choosing the correct blade size is just as important as selecting the right tooth pitch or material type. If you’re not sure what length, width, or thickness your machine requires, check out our article “How to Determine the Correct Bandsaw Blade Size for Your Machine.” It walks you through simple methods to measure your bandsaw and find a blade that fits properly—helping you avoid tracking issues, tension problems, and premature wear.
Twists in bandsaw blades can be avoided with thoughtful handling, the right pitch, and correct storage. Address issues early, follow best practices for setup, and choose your blades carefully to ensure smooth, efficient performance from your bandsaw every time.