In industries where durability and wear resistance are essential, surface hardening methods provide an effective solution. These processes strengthen a metal’s outer layer while preserving the core’s flexibility and resilience, making the metal both tough and resistant to wear. Surface hardening is vital in sectors like automotive, aerospace, and manufacturing, where parts endure constant friction and stress. This article will explore various surface hardening techniques, including induction and flame hardening, carburizing, and nitriding, highlighting their benefits and applications.
What is Surface Hardening?
Surface hardening is a technique that enhances the wear resistance of metal surfaces without compromising their internal toughness. By altering the metal’s surface properties, these methods allow parts to withstand heavy wear and tear in demanding environments.
Key methods include:
- Induction Hardening and Flame Hardening
- Chemical Composition Alteration (Carburizing and Nitriding)
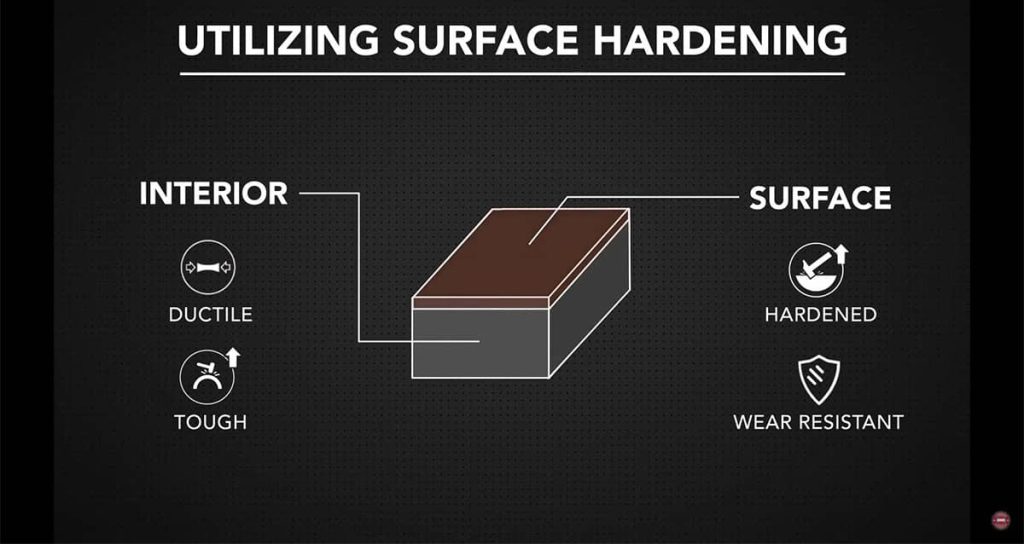
Induction Hardening and Flame Hardening
Induction and flame hardening involve heating the surface of the metal followed by rapid cooling, or quenching. Here’s how each method works:
- Induction Hardening: This technique uses electromagnetic induction to generate localized heat in specific areas of the metal. The precision of induction hardening allows operators to control the hardening depth accurately, which is beneficial for parts that need a tough surface but a softer core.
- Flame Hardening: In this process, a gas flame is applied to the metal’s surface, which is then quenched quickly. This produces a wear-resistant outer layer, making it ideal for larger, less intricate parts. Flame hardening is commonly used for items like shafts and gears that require a hardened surface to resist wear from repeated use.
Both methods are useful for creating a tough surface without affecting the metal’s overall flexibility, making them essential for heavy-duty applications.
Altering Chemical Composition: Carburizing and Nitriding
Some surface hardening methods enhance durability by changing the chemical composition of the metal’s outer layer. Carburizing and nitriding are two popular techniques used to increase hardness and wear resistance.
- Carburizing: This process involves heating the metal in a carbon-rich environment, which increases the carbon content at the surface. Carburizing results in a hardened, wear-resistant layer, while the core remains ductile. This method is widely used for gears and other components that experience heavy friction.
- Nitriding: Ideal for alloyed steels, nitriding adds nitrogen to the metal’s surface. Unlike carburizing, nitriding does not require quenching, making it a more stable process. The addition of nitrogen forms a chemically stable and wear-resistant layer, suitable for parts that demand longevity under high-stress conditions.
By altering the metal’s composition, these methods improve surface durability while preserving the metal’s core integrity, ensuring that components withstand long-term use without breaking.
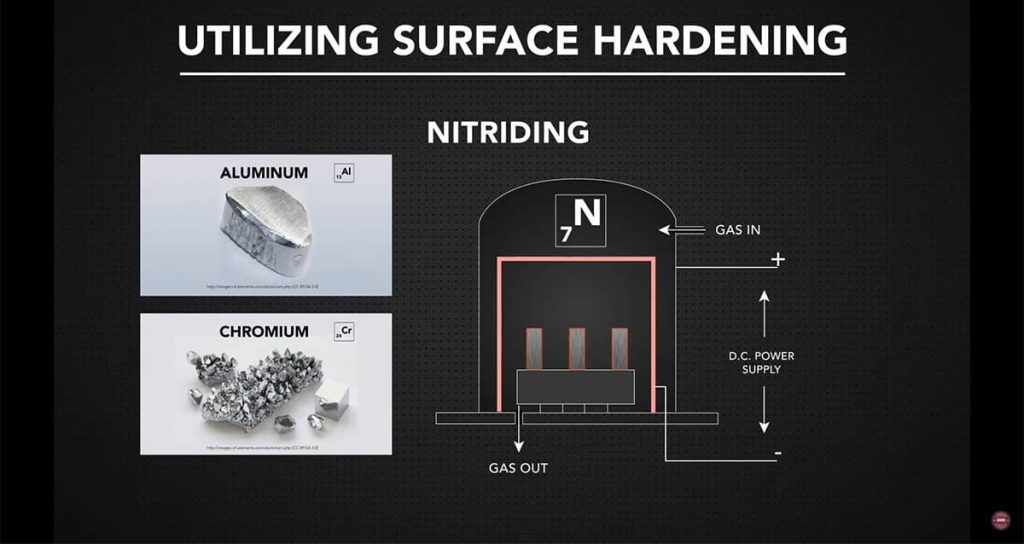
Benefits of Surface Hardening Techniques
Surface hardening offers several advantages that make metals more reliable in challenging environments. Key benefits include:
- Enhanced Wear Resistance: The hardened surface withstands abrasion, reducing wear over time.
- Core Flexibility Retained: The metal’s core remains ductile and resilient, reducing the risk of breakage under stress.
- Increased Lifespan: By resisting surface fatigue, hardened metals last longer in high-stress applications.
Practical Applications of Surface Hardening
Surface hardening techniques are widely used in various industries to improve the durability and functionality of components. Common applications include:
- Automotive Industry: Gears, crankshafts, and camshafts in vehicles are often surface-hardened to endure continuous friction and movement.
- Aerospace Sector: Components exposed to extreme temperatures and friction, such as turbine blades, benefit from surface hardening, which enhances wear resistance.
- Manufacturing Equipment: Machine parts, such as rollers and spindles, undergo surface hardening to withstand repeated, high-stress operations without deforming or wearing out.
Overview of Surface Hardening Techniques
Here’s a quick comparison of surface hardening methods to help identify the best process for various needs:
Method | Process | Suitable For | Benefits |
---|---|---|---|
Induction Hardening | Electromagnetic heating | Precise hardening in specific areas | Accurate control of hardening depth |
Flame Hardening | Gas flame and quenching | Large, less intricate parts | Creates a tough, wear-resistant surface |
Carburizing | Carbon diffusion | High-wear components | Hard outer layer with a ductile core |
Nitriding | Nitrogen diffusion | Alloyed steels, no quenching needed | Chemically stable, highly wear-resistant |
Each method has unique advantages, allowing engineers and manufacturers to choose the right process based on the specific requirements of the application.
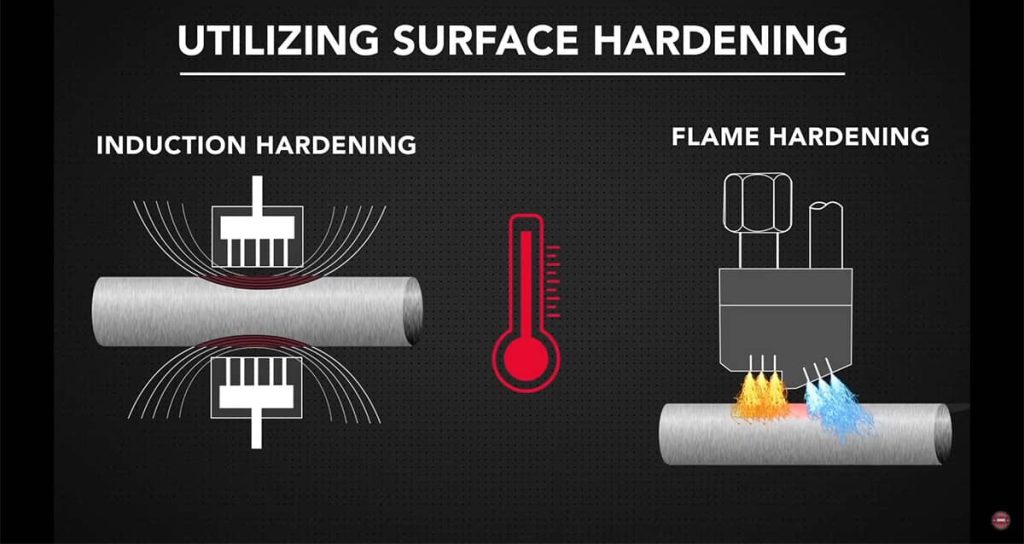
Choosing the Right Surface Hardening Technique
Selecting the best surface hardening method depends on factors such as the material, desired hardness, and specific application needs. For instance, carburizing is preferred for parts that need both wear resistance and a flexible core, while nitriding is better for components that benefit from a stable, chemically resistant surface without quenching. By understanding the options, manufacturers can make informed choices to improve product quality and performance.
Test Your Knowledge on Surface Hardening Techniques at Sawblade University!
Think you’ve mastered the fundamentals of surface hardening methods? Head over to Sawblade University and challenge yourself with our quiz on “Surface Hardening Methods: Enhancing Metal Durability and Strength.“ This interactive quiz covers key concepts, from induction and flame hardening to chemical composition alterations like carburizing and nitriding. Perfect for both beginners and seasoned professionals, it’s a great way to solidify your understanding of these essential techniques. Visit Sawblade University today and see how well you know the methods that boost metal strength and resilience!
Discover Nickel’s Melting Point and Its Role in Modern Metallurgy
Curious about the unique properties that make nickel essential in high-performance applications? Our article, “What is the Melting Point of Nickel and Its Importance in Metallurgy?“ delves into why nickel’s impressive melting point is crucial for industries like aerospace, energy, and manufacturing. Learn how this durable metal contributes to the creation of superalloys and other materials that withstand extreme conditions. Check out the full article to uncover the science behind nickel’s resilience and why it remains a top choice for demanding applications.
Surface hardening is an essential process for extending the life and resilience of metal parts. By understanding the variety of methods available, industries can enhance product durability, reduce wear, and maintain structural integrity even under extreme conditions.